How is the industrial Internet of Things influencing our factory planning?
An article by Benjamin Bielefeld, innovation manager, Head of Research & Development at HÖRMANN Rawema
In contrast with current production facilities, the factory of the future must be faster, more efficient, more sustainable and, above all, more flexible. Adaptability is a key point, and digitalisation and interconnection are crucial to this. So in keeping with the German proverb “Better to stumble on new paths than to get stuck on old ones,” HÖRMANN Rawema resolved to devote itself to the following question in a research project in 2016: What does IIoT mean for the factory and factory planning? This was aimed at ensuring that the company had its own expandable pool of data and experience to examine concepts, map out opportunities and generate its own data. The basic idea emerged: “We wanted to create a production environment that can be taken in in an instant, be equipped with a straightforward product as well as simple production steps, be set up on the basis of modules and be controlled with current industrial control systems.”
As is generally the case, the customer order process is always the focal point here. The people business is a key part of what HÖRMANN Rawema does. The following challenge arises from the already complex current issues and the trend towards even more holistic tasks: How is it possible to convey uniform goals, link up experts, ensure communication and safeguard deadlines, costs and quality for customers across all project phases? Process planners, architects, logisticians, sales staff, purchasers, specialist planners and IT staff must work as one in order to be able to implement suitable factory concepts these days. This is only possible through adept use of the opportunities of the digital world in projects.
The vision of the digital transformation of factories includes linking up the use of IIoT, AI/ML, M2M, Big Data and many other technologies that lie beneath the familiar buzzwords in a useful, efficient way in order to enable operation of a smart factory. Setting up and planning smart factories for customers is evolution, not revolution. The technology, hardware and software is now sufficiently advanced in all areas to enable efficient factories. HÖRMANN Rawema is working with its customers here to establish investment in digitalisation alongside budgets for buildings and equipment. As 3D printing still hasn't made the technological breakthrough, the conventional production technologies remain the means of choice. There is no prospect of a disruptive development that would bring about a full industrial digital transformation.
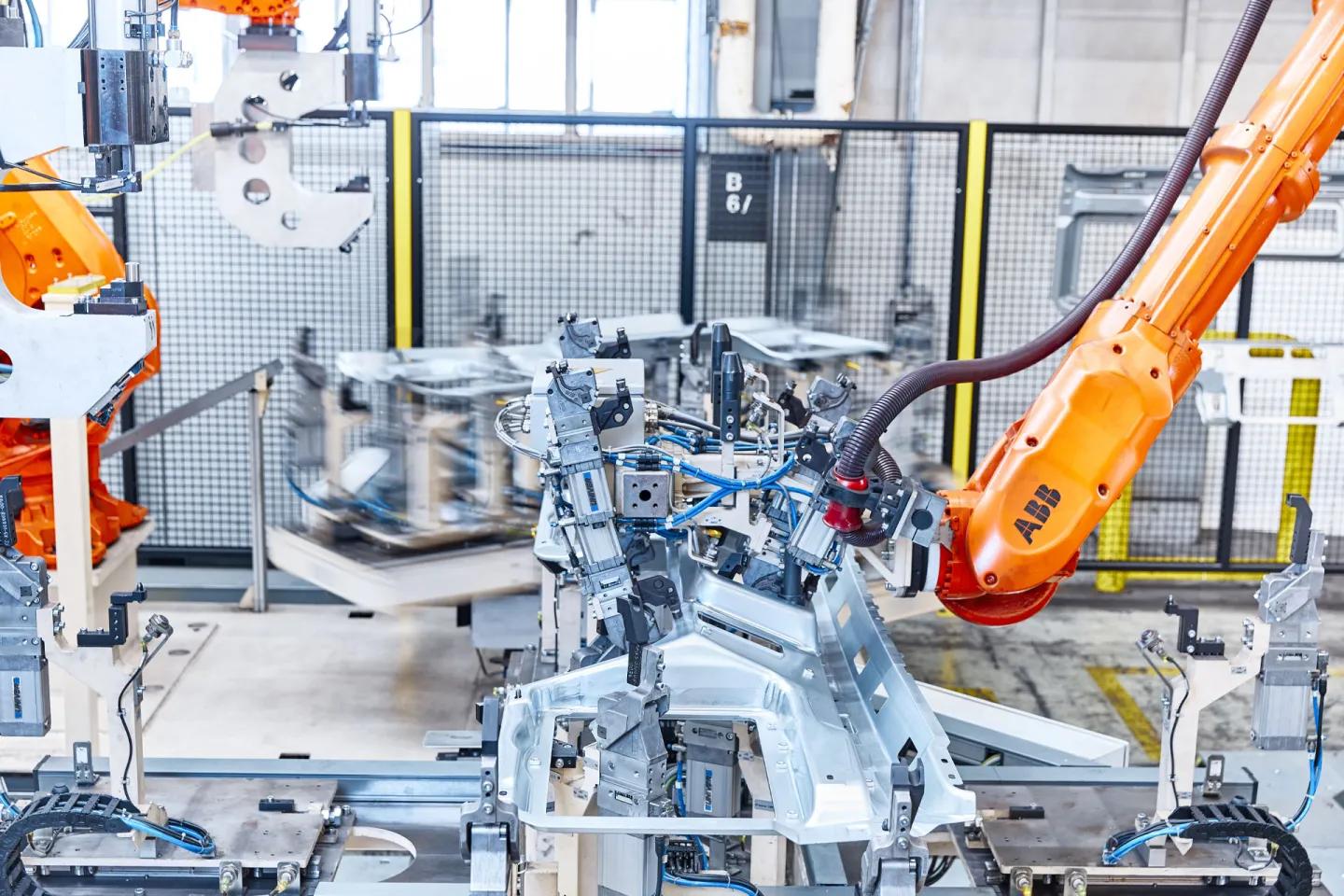
Next stages of SMART factory development
Use of modular resources
- Integration of two vehicle concepts for transportation, a sorting system and a storage system
- Adaptations for integration of data/control signals
- Integration in the monitoring concept
Integration of proprietary preventive energy management software
- Requirement-oriented inclusion and calculation of electricity consumption figures
- Creation of requirement profiles
- Integration of active regulation/control options
Expansion of display options with AR/VR
- Use of display tools suitable for industrial application
- Linking of different data sources.
For HÖRMANN Rawema, the Smart Factory innovation space in the heart of Chemnitz is a test laboratory, a condensation core, a training workshop and, of course, a showroom that is needed and is to be further expanded for research into the challenges of the industrial digital transformation and for derivation of the right tools to handle digitalisation. The factory planner represents the factory of the future from a single source. With its smart factory concept, the company secured one of the ten nominations for the 2019 Saxon Innovation Award.
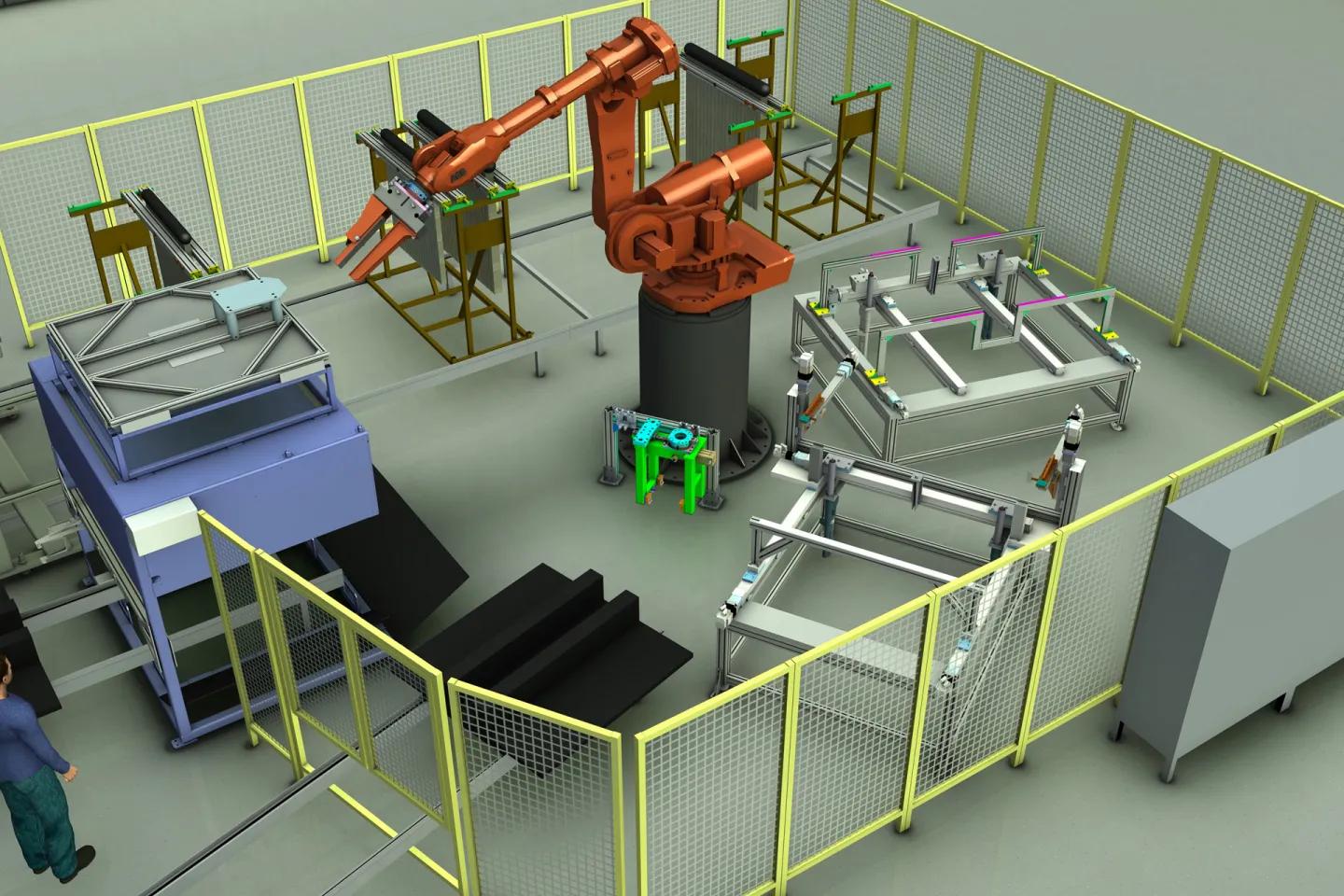